關健詞:腐植酸、配煤、制作、設備、應用
摘 要:烘干煤棒已成為型煤氣化的主流;煤棒加工制作中粘結劑的配方選型特別重要;煤棒制氣對造氣系統(tǒng)設備條件有特殊要求;煤棒制氣爐箅性能十分重要;減少制氣循環(huán)的頻繁率是降低煤棒粉化率的措施之一
1.煤棒氣化技術在煤化工行業(yè)的發(fā)展狀況:
煤化工行業(yè)是能源依賴性極強的行業(yè),而目前我國的能源狀況已經嚴重影響了煤化工行業(yè)的經濟效益,為了生存而拓寬原煤路線,尋求無煙塊煤的替代原料已經是煤化工行業(yè)無奈的選擇,同時也成為了尋求發(fā)展和降低生產成本的必由之路。
在我國將無煙粉煤制作成煤棒用于制取合成氨原料氣、工業(yè)煤氣、城市煤氣的工業(yè)化應用早已存在,只是當初應用面小和粘結劑工藝與當今有所不同,以及加工設備落后、煤棒規(guī)格不同而已。
起初講的煤棒制氣是指“清水煤棒”。清水煤棒是一種制造方法最簡單型煤,是只添加水分不摻混任何粘結劑的型煤。
上世紀70-80年代,煤棒用于合成氨廠家作為制氣原料的很少。而從上世紀90年代中后期開始,用腐植酸做粘結劑的煤棒先是在湖南,繼而在湖北等地煤化工行業(yè)開始推廣應用,而且應用面逐步向外發(fā)展,進入21世紀腐植酸煤棒氣化技術發(fā)展比較快。
湖南、湖北是兩個煤棒氣化應用大省,另外其它省份只有少量應用廠家零星分布,但是總體上講應用面呈快速擴展的趨勢,并且已經由南向北幅射,中東部地區(qū)原來采用腐植酸煤球的煤化工企業(yè),有的已經棄之改為腐植酸煤棒,其中還有幾家較大型煤化工企業(yè)。
腐植酸煤棒生產工藝相對簡單,生產設備操作比較簡便,建設施工周期短,設備投資比較少。即可以采用風干后的濕煤棒制氣,也可以烘干后入爐,因為煤棒成本相比無煙塊煤價格一般要降低30%左右,因此應用效益發(fā)揮好的廠家能較大幅度地降低生產成本。
2.腐植酸煤棒的特點 :
煤棒的成型原理與煤球有很大不同,加工過程是;經除矸、配煤、粉碎、加粘結劑+混合、堆漚、二次粉碎+混合后的熟料,由螺旋擠壓機給料口加入,由螺旋葉片推進,使粉煤不斷進一步混和、壓縮及相互擠壓揉搓。在此過程中,由于粉煤顆粒間的磨擦和粉煤與葉片以及與機殼內壁之間的磨擦,使之溫度升高,強制吸附在煤粒表面的水分和腐植酸鈉向煤顆粒的內部滲透。
由于煤顆粒反復經受揉搓、磨擦、研磨、擠壓使部分顆粒被壓潰,形成若干個細小顆粒,總體的粒度狀態(tài)小于煤球的成型粒度。從而使煤粒之間產生較大的附著力和結合力,然后擠出煤棒,經過成型過程使成型煤棒的機械強度增高。
腐植酸煤棒在應用方面已經形成了濕煤棒與烘干煤棒兩種方式;濕煤棒入爐的工作流程是,濕煤棒由成型機出來后接入周轉車內,存放風干≥24小時后再入爐,入爐時水分含量12%左右。因其水分高、表面澀性大、流動性差,采用加煤機入爐會因流動不暢而堵塞,所以目前仍然采用人工吊斗加煤。濕煤棒機械強度差,周轉和加煤過程中破損率高。而且由于入爐時煤棒水分含量高導致氣化效率低,并且每一次加煤后要先做2次左右完全上吹,利用爐內顯熱烘干煤棒快速降低水分含量,同時防止床層表面煤棒結殼,因此使煤氣爐操作程序復雜化,由于必需做幾次連續(xù)完全上吹,致使火層位置大幅度移動,影響了煤氣爐工藝狀況的穩(wěn)定性,氣化效率和熱量轉化利用率均受到不良影響。
從工藝原理上講,利用爐內顯熱烘干煤棒本身就是一種熱能浪費,而且濕煤棒由常溫猛然升高至300℃以上,煤棒內的吸附水快速向外蒸發(fā)增加了煤棒爆裂和熱粉化的量,增加了吹風帶出物的數(shù)量。另外,因為濕煤棒不能使用自動加煤,煤氣爐自動化程度降低,頻繁停爐加煤導致煤氣爐工作效率下降,單爐生產能力低。
因為濕煤棒入爐的工作流程勞動力過于密集,需要大面積的場地建防雨棚供濕煤完成風干過程,并且需要大量人力車周轉,單臺煤氣爐需要45—50輛。近些年隨著應用廠家生產規(guī)模加大,濕煤棒風干周轉量加大,使其場地和設施以及勞動力方面均難以承受。
為了解決這個問題,同時降低入爐煤棒的水分含量提高煤氣爐的氣化效率,越來越多的廠家上馬烘干裝置改用烘干煤棒。烘干煤棒應用量的發(fā)展是在隨著企業(yè)生產規(guī)模的逐步擴大而增加的。
煤棒烘干一般采用立式烘干窯或隧道式烘干窯,濕煤棒經傳送帶送入烘干爐,一般經烘干窯內動態(tài)烘干3小時左右然后送入煤氣爐氣化,入爐時煤棒溫度仍然有60℃左右,水分2%左右。濕煤棒增加烘干過程是對濕煤棒增加了一個固化、除水過程,大幅度的提高了煤棒的機械強度。煤棒烘干的熱源是利用吹風氣余熱回收后的顯熱和烘干爐上增設的煙煤燃燒爐補充烘干熱量。
烘干煤棒機械強度高,周轉和加煤過程中破碎率低,表面澀性小,入爐后床層表面分布趨于平坦,有利于改善床層透氣的均勻性,入爐后吸熱量小制氣效率高。烘干煤棒可配套使用自動加煤機,而且堆積孔隙率比中塊無煙塊煤小,床層蜜實度高。煤棒經過干燥、干餾過程后表面形成多孔結構,氣化比表面積大。加之腐植酸粘結劑也有一定的提高活性的作用,使煤棒的化學活性相應提高,有利于提高氣化強度。煤棒的外形分為三種;單圓柱形、雙柱形(即:兩根棒并連呈∞型)和梅花形(即:三根柱形棒粘連一體)。
3.氣化反應對煤棒質量的要求:
煤棒的質量要求主要有:一是物理特性;跌落測驗強度、冷抗壓強度、抗壓熱強度、熱穩(wěn)定性等。二是化學特性;化學活性、灰熔點、工業(yè)分析結果、元素分析結果等。
煤棒質量差的主要原因:
一是未按煤種特性采用相應的粘結劑配方工藝。
二是沒有根據(jù)原煤的不同特性制定合理的配煤工藝指標。
三是加工過程中沒有嚴格按煤種搭配指標的定量搭配,粘結劑也沒有按工藝要求定量加入。
四是沒能達到混合均勻。
五是企業(yè)缺乏型煤檢測手段,不能實行動態(tài)質量監(jiān)控,也不能排除管理方面存在問題。煤棒加工管理上;配煤重要性不亞于加工過程,因此兩個環(huán)節(jié)的管理都要加強。
例如有的廠配煤方面存在問題,用低灰熔點的煤和低灰熔點的粘結劑生產煤棒,造成生產中爐內經常出現(xiàn)結塊結疤現(xiàn)象,生產條件惡化。以上問題不論哪一項存在都會影響煤氣爐的氣化條件從而影響正常生產。
行業(yè)中早有“用好型煤必需先制好型煤”之說,當然煤棒制作也不例外。對腐植酸煤棒質量來說,影響煤氣爐氣化條件的主要因素不完全是煤棒的固定碳含量,而煤棒的化學活性、機械強度、熱穩(wěn)定性、灰熔點高低才是影響煤氣爐氣化條件和氣化強度及能耗高低的關健因素。單就機械強度而言,應保證烘干煤棒冷強度要達到65kg/cm2以上。
熱穩(wěn)定性差的煤棒氣化時熱粉化率高,吹風階段煤棒在高溫作用和吹風氣的沖刷下會產生一定量的粉塵,從而使帶出物增多。而且因為煤棒入爐后會出現(xiàn)爆裂,產生大量粉末使床層透氣均勻性變差,易產生偏流、上火掛壁等現(xiàn)象。
煤棒水分降低的同時機械強度提高是必然的規(guī)律,入爐煤棒水分含量是影響煤氣爐氣化效率和氣化經濟性的一項重要指標。因此,濕煤棒制氣要盡量延長煤棒周轉時間,使其水分盡量減少,入爐水分降低一是能提高煤氣爐的氣化效率;二是提高原料轉化利用率;三是能提高機械強度減少中轉和加煤過程中的破損率;四是能減少吹風帶出物;五是能減少或避免床層表面結殼,六是能有利于穩(wěn)定爐況、優(yōu)化氣化條件。要通過降低入爐煤棒的水分和通過配料時合理搭配煤種,盡可能提高煤棒的機械強度和熱穩(wěn)定性。
4.褐煤的性質和在型煤粘結劑中的作用:
我國褐煤資源豐富,1985年曾探明的儲量為1264.6億噸,占全國煤炭儲量的17.16%。褐煤有比較發(fā)達的內表面和含氧官能團,具有吸附、交換和絡合能力,是天然的廉價的吸附劑和型煤粘結劑。用于型煤粘結劑從腐植酸含量30%~40%的普通褐煤,到腐植酸含量58%以上的精制褐煤均能使用。褐煤是泥炭經過成巖階段而形成的產物,分為土狀褐煤、暗褐煤和亮褐煤。褐煤煤層中經常夾雜有保存著木質結構的植物殘骸,煤化程度淺,含碳量較低。
褐煤含碳量一般在40—60%,大部分含有40%左右的原生腐植酸,有的褐煤分析結果為總腐植酸達到53.29%,游離腐植酸=43.77%。另外還含有0.5~6%的褐煤蠟,因產地不同有的褐煤蠟含最高可達10%,揮發(fā)份含量有的達到50%左右,焦油含量因產地而異一般在3~14%,這些物質都具有很強化學活性,因而促使煤棒的化學活性提高,對提高煤氣爐的氣化強度極為有利,這也是腐植酸型煤的氣化強度大于其它粘結劑型煤的一項主要因素。褐煤的化學反應活性普遍比較高,一般在 700℃就開始氣化反應。
腐植酸鈉熔于水后形成粘稠糊狀的膠體物質,具有一定的粘結性,與煤粒經過混合、漚制后產生較強的塑性,在成型過程中受擠壓柔搓與煤粒膠合成聚合體。使煤棒具有一定的機械強度,經風干或烘干固結過程后,冷、熱強度進一步提高。煤棒入爐加溫后腐植酸鈉產生很強的吸附力,對煤粒產生較強的聚合力和吸附力形成骨架作用使之熱穩(wěn)定性提高。
在型煤加工制作中,粘結劑的配方選型特別重要,采用有機粘結劑制成的型煤冷強度較高,但是熱強度和熱穩(wěn)定性都比較低。采用無機粘結劑可使型煤具有較高的熱強度和熱穩(wěn)定性,但是會引起型煤固定碳降低。而腐植酸粘結劑的性質介于有機粘結劑和無機粘結劑之間,屬于復合型粘結劑可以彌補二者的不足,可以使型煤達到較高的抗壓強度和熱穩(wěn)定性,而不會使型煤固定碳含量有大的降低。(附表:型煤粘結劑分類)
粘結劑型煤分類:
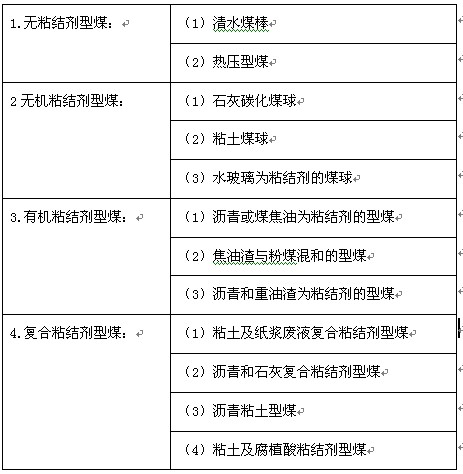
5. 腐植酸煤棒的制作中的配煤要求:
要求多選用反應性強的煤(化學活性好的煤)以保證在氣化和燃燒過程中反應速度快、氣化效率高。原煤的反應性強弱還直接影響煤氣爐的耗煤量、發(fā)氣量、熱轉化利用率以及煤氣中的有效成份含量等。
腐植酸煤棒配煤有四個重點;
a.科學合理的制定配煤工藝
b.嚴格執(zhí)行配煤定量
c.破碎到合理粒度
d.與粘結劑充分混合
煤棒的抗碎強度和熱穩(wěn)定性與所用的無煙煤煤種有很大的關系,配煤時既要考慮原料煤的固定碳、化學活性等指標,又要考慮成型后煤棒的機械強度和熱穩(wěn)定性。加工工藝條件一定時,不同煤種制成的煤棒冷抗壓強度差別很大,這是由于煤本身具有的物理化學性質不同所致。而且固體煤粒的水份含量和不同煤種表面物理化學性質不同,其最高內在水分也不同,因此對煤的成型性有也一定影響。
山西粉煤固定碳含量高,化學活性有好有差,選擇的余地較大。但是,大部分山西煤為砂巖性,結構致密、機械強度高、擠壓成型時反彈性大,親水性差、親合力差、揮發(fā)份含量低。因此,成型效果不好,一般來講機械強度高的無煙塊煤產生的煤粉都有原本特征。這種特性的煤適合與較強粘結性、土性灰質、灰熔點較低、揮發(fā)份偏高的煤搭配。因為砂性煤必需配入部分冷粘結性強的粘土性灰質的無煙煤,同時要盡可能選用揮發(fā)份及硫含量達標的煤種。
腐植酸煤棒的灰熔點、成渣性是煤棒氣化的重要指標,灰熔點低的煤棒在氣化過程中容易結疤結塊,因此要求煤棒灰熔點盡可能提高。國標規(guī)定固定層氣化用煤的灰熔點要≥1250℃,由于型煤灰分一般≥25%,灰份含量高、灰熔點又低的原料操作難度是極大的,所以煤棒的熔點最好要≥1300℃。
煤棒的灰熔點主要取決于原煤的灰分組成和粘結劑成分組成。無煙煤的灰分物質組成及含量差異較大,因此要進行科學搭配,煤中的灰份組成主要是氧化鋁(A12O3)、二氧化硅(SiO2)、氧化鉀(K20)、氧化鈉(Na0)、氧化鎂(MgO)、氧化鈣(CaO)、氧化鐵(FeO)、有機硫(S)。
原料煤中氧化鋁、氧化鐵、有機硫是低燃點物質、又是低熔點物質。它們對型煤的影響只是對煤棒的灰熔點有直接影響,它們的含量越高煤棒的灰熔點越低。對煤棒化學活性產生直接影響的是“揮發(fā)份”,成品干煤棒中揮發(fā)份含量應在7%左右為宜,這樣即不會因揮發(fā)份含量低影響化學活性,也不會因為揮發(fā)份含量高而影響煤氣質量。
不同變質程度的煤,其灰份組成有較大的差異,體現(xiàn)出不同的灰熔點。當使用低灰熔點的無煙粉煤生產煤棒,必須要添加高熔點無煙煤粉和高熔點點添加劑才能使煤棒的灰熔點達到要求的指標,例如添加粘土(陶土)。粘土資源豐富、價格低廉,粘土本身無可燃物質,主要礦物成份是硅,灰熔點較高,一般在1400—1450℃。但是,因其不含可燃的活性物質所以無反應活性,在添加中要制定合理指標。過量添加粘土后雖然增加煤球的灰熔點和機械強度,但是也相應降低了型煤的含碳量和氣化反應活性。
6.簡述腐植酸鈉煤棒制作步驟:
第一步是腐植酸溶液的制備,粘結劑的含量高低和粘結劑質量的優(yōu)劣在一定程度上決定了煤棒質量,用純堿(Na2CO3)或燒堿(NaOH)溶液抽取褐煤中所含的腐植酸,通過堿和酸中和成腐植酸鈉鹽溶于水中作粘結劑,通過復分解反應,腐植酸變成鈉鹽溶于水中,而碳酸根則和鈣離子結合生成碳酸鈣沉淀。
第二步;原料煤要經過除矸、篩選、配煤、粉碎、一次攪拌、腐植酸鈉粘結劑加入、漚制。堆漚是為了讓水分和腐植酸鈉充分滲入煤粒,漚制時間應≥24小時,一些廠家漚制時間達48小時使的溶合效果進一步提高,對提高煤棒質量當然是有益的。下一步是二次粉碎、攪拌+深度混合至擠壓成型。
配煤完成后,煤棒加工質量的關鍵就在于是否采用了先進的高效粘結劑、混合攪拌工藝和先進可靠的成型設備及烘干設備。配煤完成后開始粉碎和混合,對于原煤的粉碎粒度也有一定要求,粉碎粒度過細,需增加粘結劑量增加成本,降低機械強度,降低含碳量。
混合方法也有所不同;有的先粉碎后混合,將煤沫一次破碎到3mm以下,再用雙輥混合攪拌機混合,這樣很難達到理想的混合效果。應該把破碎與混合作為一個過程;先將粘結性與煤沫混合在一起粉碎至<5mm,進入混合攪拌機與配好的粘結劑充分混合攪拌,堆放≥2小時,再二次混合粉碎至3mm以下。
7.煤棒制氣對造氣系統(tǒng)設備配套條件方面的要求:
事物總有它的多源性,雖然強調說型煤制作的重要性高于型煤操作的重要性,但這只是強調事物起源的重要性,倡導原料問題務必從源頭抓起,為造氣生產創(chuàng)造原料基礎。
然而,一個企業(yè)僅僅是型煤質量提高了,只是造氣生產良性化發(fā)展的決定因素之一。如果;a、造氣技術裝備條件落后。b、系統(tǒng)配置沒有側重型煤氣化的技術要求。c、現(xiàn)行工藝指標不適合型煤氣化條件要求。b、仍然按照無煙塊煤的操作方法和習慣去操作等。
一套造氣系統(tǒng)如果存在上述問題之一,就會限制生產潛力挖掘,直接影響型煤氣化的效益發(fā)揮。一些企業(yè)就是因為存在以上某一原因得不到根治而放棄使用型煤。
腐植酸煤棒必竟屬于粉煤成型,它的固定碳含量和機械強度,以及熱穩(wěn)定性等理化特性與一般質量的無塊煤相比都差距較大。因此,要依據(jù)煤棒的氣化應用特點,在造氣系統(tǒng)平衡配套方面采取有效措施。
7.1. 要想提高煤棒氣化的氣化強度和經濟性,煤氣爐的三個高徑比一定要合理。從工藝角度講;床層高度是造氣其它工藝條件優(yōu)化的基礎,如果不具備此條件,其它工藝的調整都必將成為圍繞現(xiàn)有條件所做的彌補之術。
7.2.煤棒氣化過程中吹風帶出物較多,對煤氣爐吹風氣除塵器和煤氣除塵能力要求比塊煤要高。洗氣塔負荷也重了,因此洗氣塔凈化能力需要增加20%。
7.3.力求穩(wěn)定入爐蒸汽的壓力和流量,首先入爐蒸汽網絡一定要配置合理;傳統(tǒng)的單爐一鍋(廢熱鍋爐)、一塔(洗氣塔)、一罐(蒸汽緩沖罐)的配置條件已經極少存在了,新上馬的和新改造的系統(tǒng)一般都是四臺煤氣爐配一個鼓風機、一個緩沖罐、一套蒸汽調節(jié)閥組的綜合余熱回收流程。而對于煤棒氣化來講,僅是這樣的話是不夠的。至少必須加一套入爐蒸汽調節(jié)閥組,保證兩臺爐一個補氣點。按目前的煤氣爐生產能力,四臺爐用一個蒸汽緩沖罐,在如此大流量的條件下,僅靠蒸汽緩沖罐的作用并保證不了入爐蒸汽穩(wěn)定性,如果沒有多個補償能力大的補氣點是不行的。
雖然設計中增大了蒸汽緩沖罐容積,但是在目前大負荷生產的條件下,大大超出了原設計的單位時間內的單爐入爐量。加之四臺煤氣爐用一臺蒸汽緩沖罐,勢必造成兩臺煤氣爐屬于遠程輸送入爐蒸汽,必然存在補償能力差的問題,勢必因補償能力差制約瞬時流量。
7.4. 工藝管線配置,從氣化條件方面講,煤棒因其固有的理化特性因素影響,風速、風量無法提高到優(yōu)質無煙塊煤的程度。因此,專門的煤棒氣化系統(tǒng)在設備配套條件方面除煤氣爐主體的三個高徑比以外;煤氣管道、空氣管道、配套閥門等方面,均不宜過大,不能效仿無煙塊煤氣化系統(tǒng)。因為實際運行中,煤棒氣化一般都與中等以上質量的無煙塊煤相比,單爐發(fā)氣量一般要降低20%左右,這是眾多廠家生產實踐驗證的結果。
煤棒氣化的造氣系統(tǒng)要提高單爐生產能力,只有將煤氣爐本身配置加大,以增加單爐生產能力,這樣才能有效的彌補煤棒氣化的弱勢。如果煤氣爐本體配置能力小,單爐消化能力更小,更遠離了經濟運行的氣化條件。
7.5. 煤棒氣化配套的風機能力,應區(qū)別開濕煤棒、烘干煤棒和床層厚度等不同的條件特點。
因煤棒灰分含量比較高,入爐煤棒的粒度差別比較大,床層孔隙率各環(huán)區(qū)差別比較大,各環(huán)區(qū)阻力差距必然比較大,外環(huán)區(qū)床層阻力小,不適合高風速。在同樣直徑的煤氣爐上煤棒氣化的條件下,風量選擇宜比無煙塊煤風量小50m3/㎡.min為宜,而且風機壓頭應選26kpa左右為宜。
7.6.使用專用爐箅:煤棒的床層表面及床層內部的物料分布是獨具特點的。濕煤棒氣化時:因濕煤棒水分含量高和型狀特點所致,其表面澀性大、流動性差。因此,炭層表面中心區(qū)峰點與邊緣區(qū)的位差很大,加之加煤和周轉過程中產生的碎細料和煤粉集中于中心區(qū),因而各環(huán)區(qū)的阻力差比較大。
烘干煤棒在周轉和烘干過程中部分產生斷裂,雖然直徑未變,但是長度很不規(guī)整,從而形成了獨有的粒度特點。入爐后小粒度的煤棒集中在中心區(qū),稍長一點的停滯在內環(huán)區(qū),再長一些的煤棒則滾落到煤氣爐的外環(huán)區(qū)。三個環(huán)區(qū)被三種不同粒度的煤棒所充實,因而同一截面上阻力不均等。但是,烘干煤棒表面澀性小于濕煤棒,床層表面分布趨于平坦,中心區(qū)阻力小于濕煤棒。由于上述各種不同特征存在,所以要求爐箅布風條件必需適合其各自不同的床層分布特點,如果不專門設計爐箅布風條件就能造成入爐氣化劑產生環(huán)狀偏流或局部偏流。
因為三個環(huán)區(qū)的阻力很不相等,爐箅布風設計上必需將阻力大的區(qū)域相應加大通風量,去克服局部阻力,通過強制通風提高阻力大的區(qū)域的火層溫度。相反,通風阻力小的區(qū)域,必需相應控制其通風量控制其溫升速度,從而控制在同一截面上火層溫度基本相等,這就是專用爐箅的作用體現(xiàn)。
腐植酸煤棒成渣性強,正常運行中形成的灰渣比較酥軟,但是其單位時間內的排灰量要大于中等質量以上的無煙塊煤,這是因為煤棒的固定碳含量低所致。因此,爐箅設計就必需要根據(jù)此特點確定合理的排灰面積,保證爐條機轉速在適中的運轉下,就能保證物料平衡,從而保證爐內有正常的成渣條件和有序的排除能力。
煤棒制氣的煤氣爐有時也會出現(xiàn)結塊、結疤的現(xiàn)象,甚至大疤塊因不易破除而在爐內轉動,遇到此情況被迫停爐息火人工破除。也有的是偏火偏灰經常出現(xiàn),甚至經常出現(xiàn)一側排渣口堵塞。
一系列問題的原因:
一是與原煤質量或煤棒加工質量有關。
二是與工藝條件或操作合理性有關。
三是也與爐箅的布風條件合理與否有關。
四是與爐箅的破渣能力大小也有一定關系。
五是與配套的破渣條規(guī)格和定位是否經過專門設計有一定關系,因為破渣條與爐箅的配合間隙確定了破渣粒度大小。
六是與防流方法有一定關系,這些問題都是爐況穩(wěn)定和優(yōu)化的影響因素和制約因素。
因此,要求爐箅的布風條件必需要與煤棒理化特性相適應,破渣能力要強,破渣粒度要與排灰口高度相適配,以上條件都是煤棒專用爐箅的必備條件。具備了以上條件,煤棒制氣才能穩(wěn)定爐況,才有條件進一步優(yōu)化工藝。
8. 煤棒氣化的工藝條件選擇
氣化煤棒的生產應用要點是;
① 系統(tǒng)技術裝備必需適合煤棒的氣化特點。
② 制訂的工藝指標必需適合煤棒的氣化特點。
③ 確定的工藝指標必需抓住技術要領的關鍵控制點。
④ 操作方法的科學性必需適合原料特性和設備狀況。
⑤ 按造氣“四穩(wěn)操作法”的操作理念,工藝操作的穩(wěn)定性尤為重要,這一方面受制于操作控制水平和專業(yè)管理水平。
原料條件和設備配套條件具備相應水平后,就要進入更關鍵的工藝操作環(huán)節(jié)。雖然都強調型煤加工質量的重要性,但這只是為了消除根源性因素的影響,為造氣生產提供必需的原料條件。但是屢見不鮮的是原料條件和設備配套條件相比較好的條件下,生產運行狀況卻一塌糊涂。
所以說,造氣生產是一個多源性的系統(tǒng)工程,同樣的原料條件、同樣的裝備水平,但是造氣生產的運行狀態(tài)和經濟性的差距卻總是相差很大。反之原料和裝備條件相比較差的單位,生產水平與之相比卻存在較大的反差,如此事例同樣屢見不鮮。
造氣工藝、操作、管理中蘊藏的潛力最大,一個企業(yè)應提高應用技術水平,倡導“以人為本”,因為人的潛力是最大的,人的潛能是能夠隨著不斷的學習和積累被不斷激發(fā)而提高的。
8.1. 負荷控制:
創(chuàng)造條件多加負荷,提高單爐生產能力。人們都知道改用型煤氣化,單爐生產能力會下降,因此備用爐少的廠家改用型煤氣化之前都新增幾臺煤氣爐。備用爐多的廠家也早作準確,需要增開幾臺就增開幾臺。然而,型煤氣化與無煙塊煤氣化一樣,單爐生產能力的調整彈性很大。小負荷、大爐群的生產模式無法達到高產低耗。腐植酸煤棒氣化應用效果好、經濟效益高的廠家都是經過堅苦攻關才最終實現(xiàn)了高負荷生產、長周期穩(wěn)定的生產局面,經濟效益正是因此而產生。
腐植酸煤棒氣化條件要求;床層高度應在設備條件允許的前提下盡量達到床層高徑比。以增加蓄熱能力,并且要盡可能采用高爐溫制氣,從而提高氣化效率,優(yōu)化煤氣成份。
造氣生產要倡導從實際出發(fā),用實踐檢驗真理,不要總是拘泥于理論計算。因為造氣生產中影響的動態(tài)因素多,理論計算與應用的實際情況相吻合的幾率不高,甚至有時偏差很大,這是有目共睹的事實。因此,從事造氣的具體工作絕不能完全拘泥于理論算計上,理論指導實踐這句話一點也不錯,但是指導造氣生產的理論應該是來源于生產實踐,應該是經過驗證并升華了的、不拘一格的、求真務實的創(chuàng)新型理論。
例如;從原則上說吹風時間越短越好,但是要在短時間內完成必需的送風量,要建立在必需具備的原料條件和床層高度基礎上。吹風過程的長短、風量的大小應該完全取決于床層高度和原料的承受能力,除了要有足夠的床層高度外,還受原料的機械強度、熱穩(wěn)定性和粒度大小及均勻性的限制。腐植酸煤棒制氣,在風機選擇和使用上的原則應該是“低風壓、大風量”。
采用機械強度和熱穩(wěn)定性好,并且粒度相對均勻的燃料可適當提高空氣流速;反之應適當降低空氣流速。特別是煤棒制氣,如果采用高風壓大風量吹風,勢必造成煤棒粉化加劇。而且由空氣流速快,床層吹翻或產生風洞的幾率增加,吹風氣帶出物明顯增多。因此,實際生產中要根據(jù)燃料性質來決定是延長吹風時間,還是提高空氣流速來達到增加吹風量的目的。
要充分挖掘設備、原料、人員的各方面潛力,在條件允許的條件下,盡量將制氣負荷提至高限。并且要通過技術改造不斷消除制約因素,創(chuàng)造條件逐步提高氣化強度。氣化層溫度越高越能加大氣化能力,加快成渣速度并提高成渣率、提高氣化效率。成渣是對灰份的濃縮,如果成渣率低,灰渣中含碳量必定高。
然而,任何一種事物發(fā)展到極限狀態(tài),對操作控制都會產生一定的難度和危險性。因此,氣化負荷要確定合理,不能超出設備、原料和人力資源的最大能力。
8.2.恰當?shù)难h(huán)時間分配
腐植酸煤棒在氣化過程中粉化的主要原因包含以下幾點;
一是煤棒質量的因素。
二是入爐前后的溫差過大。
三是階段轉換造成床層表面溫度變化幅度過大,峰谷值之差拉大。
上行氣溫度與下吹入爐蒸汽溫度之差越大對原料冷激影響的程度越大,冷激作用主要是在下吹初始階段。
那么,減少制氣循環(huán)的頻繁率是降低煤棒粉化的有益措施之一,而且是簡單易行、行之有效的措施,這一方面的影響因素正是煤棒氣化不宜采用短循環(huán)的原因之一。煤氣爐三個高徑比合理的條件下,∮2800煤氣爐宜采用145—150s循環(huán)時間,∮2610左右的煤氣爐(∮2600、∮2610、∮2650)循環(huán)時間135s為底限,120s循環(huán)時間僅限于∮2400煤氣爐使用。
“慣性思維是技術創(chuàng)新的最大障礙”,煤氣爐已經逐步走向大型化了,系統(tǒng)技術裝備也已經今非夕比了,再不能不論什么原料條件、不論什么技術裝備條件、不論存在什么問題,總是用120s循環(huán)時間去以不變應萬變了。
實際生產中,合理確定循環(huán)時間對穩(wěn)定爐況、提高原料的轉化利用率,減少熱損失和提高制氣效率能起到很重要的作用。
8.3. 合理的入爐蒸汽溫度和用量
腐植酸煤棒氣化必須用過熱蒸汽,而且對入爐蒸汽溫度的要求區(qū)別于無煙塊煤。由于烘干煤棒本身特性決定了在正常負荷的條件下,上、下行氣體溫度不能象中小塊無煙煤那樣降的那樣低,特別是上行溫度不會象中小塊煤氣化那樣降低到200℃左右。為了減小蒸汽入爐時床層表面溫度的峰谷值之差,煤棒氣化時的入爐蒸汽溫度必需提高至與上行溫度控制的基本值相仿。那么,煤棒制氣時入爐蒸汽溫度應控制在300℃左右為宜。
腐植酸煤棒在氣化原料行列里屬劣質原料,由于熱穩(wěn)定性、化學活性、灰熔點等方面都相比較差,因此氣化層溫度自然要低于優(yōu)質塊煤。所以對于劣質原料來講不能過度追求蒸汽分解率,否則就會造成發(fā)氣量小、熱損失大,原料煤的轉化利用率低。
造氣工藝技術講究“蒸汽分解率”與“蒸汽分解量”的平衡問題,對于煤棒氣化來講,不適合刻意追求提高蒸汽分解率,而應該以充足的蒸汽用量促使蒸汽分解量提高,從而提高煤氣爐氣化能力,而且有利于上下行氣體溫度的控制和提高灰渣質量。這就是以一定的蒸汽損失換取發(fā)氣量提高、生產穩(wěn)定、對綜合效益是很有利的,這也是在此原料條件下權衡利弊后的無奈之舉。其實這一操作特點在多數(shù)應用煤棒的單位已經存在,劣質原料制氣蒸汽分解率低于優(yōu)質無煙塊煤、蒸汽消耗高于優(yōu)質無煙塊煤,這是原料特性所決定的,已經成為必然現(xiàn)象。
結束語:
目前,雖然大多數(shù)使用煤棒造氣的煤化工企業(yè)確實因此帶來了可觀的經濟效益,但也有一些企業(yè)由于種種原因經濟效益的發(fā)揮不盡理想,甚至有的企業(yè)因此而使生產陷入被動局面。
型煤氣化在煤化工行業(yè)的原料結構中所占比重越來越大,烘干煤棒也已經成為型煤氣化的主流。而在這一課題當中;專用設備技術開發(fā)、生產系統(tǒng)平衡配套技術、工藝指標和操作方法等方面仍然有進一步開發(fā)和挖掘的潛力。因此,在加大型煤氣化工藝技術研究開發(fā)的同時,應該加快煤氣裝備制造業(yè)的新技術開發(fā)速度,提高其創(chuàng)新開發(fā)能力,促進型煤專用技術裝備的性能提高,特別是核心技術方面的革新改造,要盡快推出“創(chuàng)新型專用系統(tǒng)裝備”應用到型煤氣化生產系統(tǒng)當中去,從而進一步提高生產系統(tǒng)的技術裝備水平,增強生產裝置的節(jié)能降耗功能。
絕大多數(shù)煤化工生產企業(yè)幾十年來的主要精力都放在無煙塊煤氣化技術上了,型煤氣化對于大多數(shù)廠家來講都是新課題。如今,應用和關注這項技術的人越來越多,實踐證明只要業(yè)內大多數(shù)人共同努力的事情必然會有成功進展,在業(yè)內同仁的共同努力下,型煤氣化技術必將有新的突破。